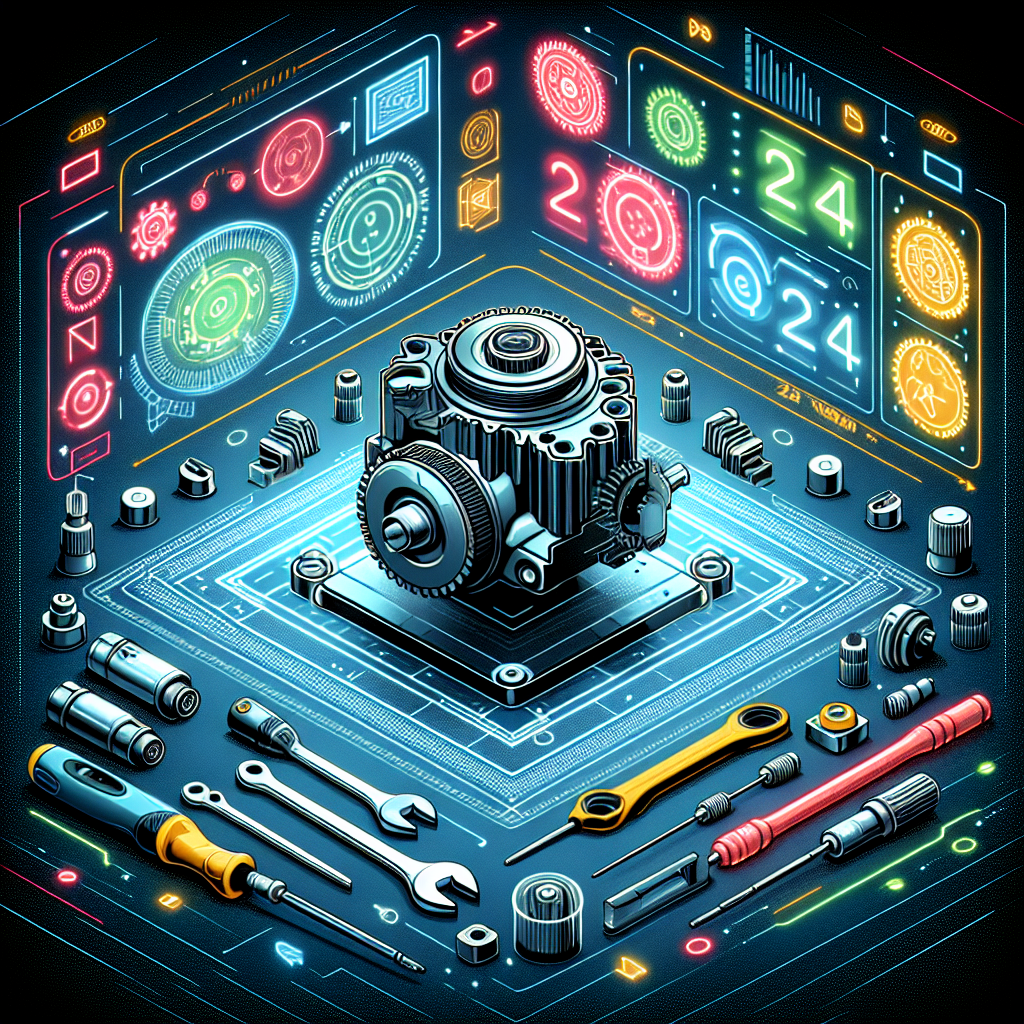
Introduction
In the world of automotive engineering, the Honda K24 engine stands as a paradigm of performance and reliability. However, one of the critical components ensuring its optimal function is the crank sensor. Understanding how to wire a K24 crank sensor can save you time, money, and a whole lot of headaches. This guide will walk you through the process, step by step, ensuring that even those relatively new to car mechanics can follow along.
What is a K24 Crank Sensor?
A crank sensor, also called a crankshaft position sensor, monitors the position and rotational speed of the crankshaft. This information is vital for the engine control unit (ECU) to manage ignition timing and fuel injection, leading to smooth engine performance. A malfunctioning crank sensor can result in poor performance, stalling, or even prevent the engine from starting.
Tools and Materials Needed
Before diving into the wiring process, gather all the necessary tools and materials:
-
Tools:
- Socket wrench set
- Screwdrivers
- Wire strippers
- Soldering iron and solder
- Multimeter
- Electrical tape
- Heat shrink tubing
- Zip ties
- Materials:
- New crank sensor (if replacement is needed)
- Wiring harness (compatible with K24 engine)
- Electrical connectors
Having these items on hand will ensure that you don’t have to stop midway to search for a tool or a component.
Step-by-Step Instructions
Step 1: Disconnect the Battery
Safety first! Always start by disconnecting the battery to avoid any electrical mishaps. Use a socket wrench to remove the negative terminal from the battery.
Step 2: Locate the Crank Sensor
The K24 crank sensor is usually located at the front of the engine near the crankshaft pulley. Refer to your vehicle’s manual or this detailed guide for exact location specifics.
Step 3: Remove the Old Crank Sensor
- Unscrew Bolts: Use a socket wrench to remove the bolts securing the crank sensor.
- Disconnect Wiring: Carefully unplug the wiring harness connected to the sensor.
Step 4: Prepare the New Sensor
- Inspect the Sensor: Ensure that the new sensor is compatible with your K24 engine.
- Attach Wiring Harness: Connect the new wiring harness to the sensor.
Step 5: Wiring the Crank Sensor
Identify the Wires
Typically, a K24 crank sensor has three wires:
- Power (usually red or black with a white stripe)
- Ground (black)
- Signal (varies)
Connect the Wires
- Strip the Wires: Use wire strippers to remove a small section of insulation from each wire.
- Solder Connections: Carefully solder the corresponding wires from the sensor to the wires in your engine’s wiring harness. Use heat shrink tubing to cover soldered joints for protection.
- Secure Connections: Wrap connections with electrical tape and use zip ties to keep the wiring neat and secure.
Step 6: Reinstall the Sensor
- Position Sensor: Place the new crank sensor in the same location as the old one.
- Secure Bolts: Use a socket wrench to bolt the sensor into place.
- Reconnect Harness: Plug the wiring harness into the sensor.
Step 7: Reconnect the Battery
Reconnect the negative terminal to the battery and tighten it securely.
Step 8: Test the Installation
- Start the Car: Turn on the ignition to see if the engine starts smoothly.
- Check for Error Codes: Use a diagnostic tool to ensure no error codes are present.
Congratulations! You’ve successfully wired your K24 crank sensor.
Troubleshooting Tips
Despite following the steps meticulously, you may encounter issues. Here are some troubleshooting tips:
- Check Connections: Ensure all wires are securely connected.
- Verify Sensor Compatibility: Double-check if the sensor is compatible with your K24 engine.
- Test Voltage: Use a multimeter to check the voltage levels at different points.
For further guidance, check out this troubleshooting resource.
Why Proper Wiring is Important
Proper wiring of your K24 crank sensor is crucial for a couple of key reasons:
- Optimal Engine Performance: Accurate crankshaft position information ensures the engine runs smoothly.
- Fuel Efficiency: Precise timing of fuel injection increases fuel efficiency.
- Avoids Engine Damage: Incorrect wiring could lead to engine misfires or more severe damage.
Common Mistakes to Avoid
Avoiding common pitfalls can make the difference between a successful installation and a frustrating one:
- Incorrect Wire Identification: Mixing up the power, ground, and signal wires can cause malfunctions.
- Poor Soldering: Cold solder joints can result in intermittent connections.
- Ignoring Error Codes: Always check for error codes after the installation.
Maintenance Tips
To maintain your K24 crank sensor in optimal condition:
- Keep it Clean: Regularly inspect for dirt or oil buildup.
- Check Wiring: Periodically ensure all connections are secure.
- Monitor Performance: Pay attention to any changes in engine behavior.
Advanced Techniques
For those confident in their mechanical abilities, exploring advanced techniques such as diagnostic tuning can further refine engine performance. These techniques involve using specialized tools to tweak the ECU settings based on the crank sensor’s feedback.
FAQs
Q1: How do I know if my crank sensor is faulty?
A faulty crank sensor often results in engine misfires, stalling, or a lack of responsiveness when you turn the key. Using a diagnostic tool to check for error codes can confirm the sensor’s condition.
Q2: Can I drive with a bad crank sensor?
While you may still drive with a faulty crank sensor, it is not advisable. The engine’s performance will be compromised, and it could result in more severe damage over time.
Q3: How often should I check the crank sensor wiring?
It’s a good practice to inspect the crank sensor and its wiring during regular maintenance checks, typically every six months or whenever you notice performance issues.
Q4: Can I replace the crank sensor myself?
Yes, replacing a crank sensor is a feasible task for DIY mechanics with the proper tools and instructions. Following a detailed guide, like the one above, will facilitate the process.
For more in-depth automotive guides, visit this comprehensive site.
Conclusion
Wiring a K24 crank sensor doesn’t have to be a daunting task with the right knowledge and tools. This guide has walked you through each step to ensure a successful installation. Remember, attention to detail and patience are your best friends in this process. So, gather your tools, follow the steps, and get your engine running smoothly again!