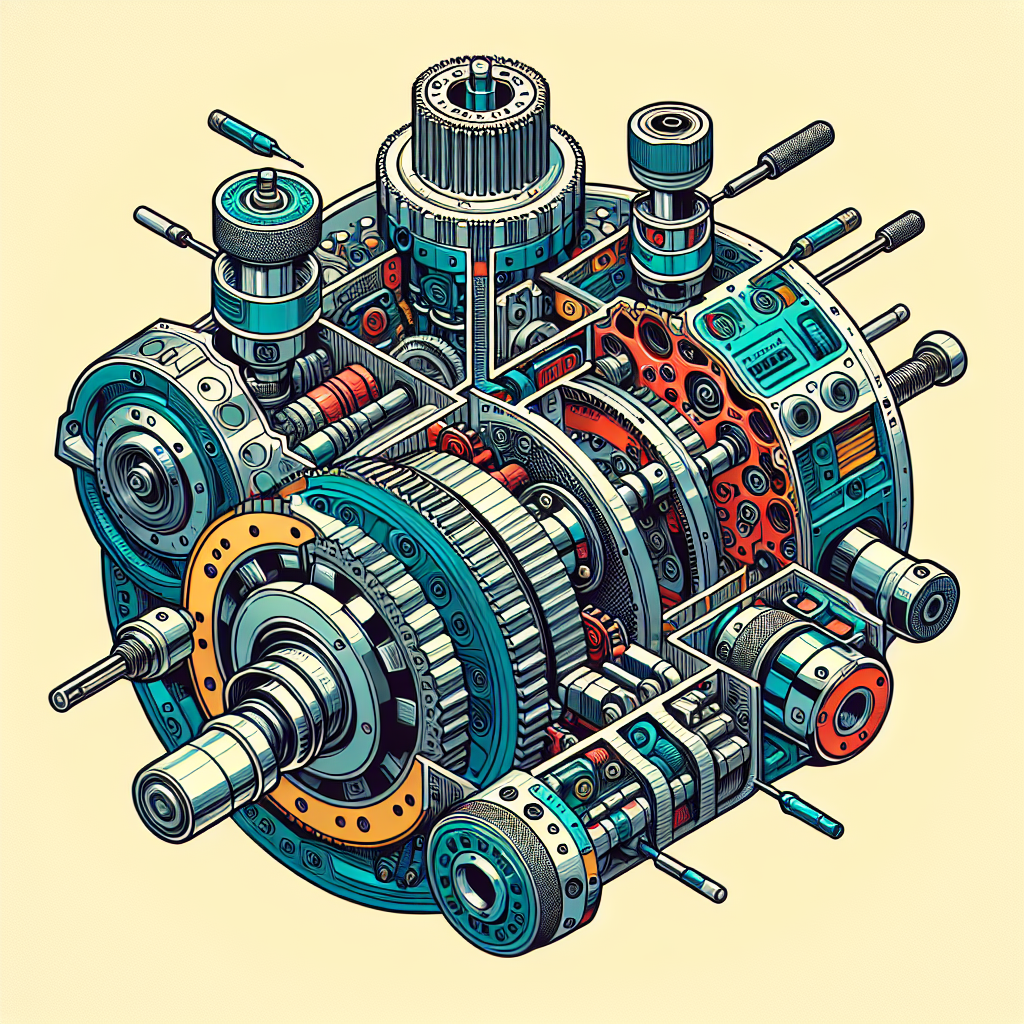
Introduction
Crankshaft position sensors are integral to modern automotive systems, influencing engine timing and overall vehicle performance. Having first-hand experience, I can attest that understanding and using a crankshaft position sensor diagram is crucial for achieving optimal engine functioning. This article will walk you through a comprehensive guide, detailing every aspect related to these sensors – from basics to advanced troubleshooting.
What is a Crankshaft Position Sensor?
The crankshaft position sensor, often abbreviated as CKP or CPS, is a crucial engine management component. It monitors the position and rotational speed of the crankshaft. Recognizing the sensor’s role can significantly improve your approach to diagnosing engine issues.
Importance of the Crankshaft Position Sensor
Engine Timing and Efficiency
The crankshaft position sensor provides real-time data to the Engine Control Unit (ECU), ensuring precise engine timing and efficiency. Any malfunction in this sensor can lead to poor engine performance, meaning timely repairs and understanding the sensor diagram are essential.
Synchronization with Camshaft Position Sensor
The crankshaft position sensor works in tandem with the camshaft position sensor to synchronize the engine’s timing, ensuring that the fuel injectors and spark plugs fire at the correct intervals. This synchronization is vital for optimal performance.
Components of a Crankshaft Position Sensor
Knowing the components helps in deciphering the crankshaft position sensor diagram effectively:
Magnetic Pick-up
It generates a voltage signal as the teeth of a reluctor pass by the sensor.
Reluctor Wheel
This toothed wheel is attached to the crankshaft, and its rotation triggers the magnetic pick-up.
Wiring Harness
It connects the sensor to the ECU, transmitting the signals.
Mounting Bracket
This ensures the sensor is positioned correctly near the reluctor wheel.
Reading a Crankshaft Position Sensor Diagram
Basic Layout
A typical crankshaft position sensor diagram includes the following elements:
- Power supply (12V)
- Ground connection
- Signal output
Below is a simplified layout for better understanding:
Component | Description |
---|---|
Power supply | Provides the necessary voltage to operate the sensor. |
Ground | Establishes a reference point for electrical circuits. |
Signal output | Sends the crankshaft position data to the ECU. |
Wiring Color Codes
Different vehicles may have varying color codes for the wiring. Refer to your specific vehicle’s service manual for accurate details. Websites like AutoZone frequently have these manuals available.
Common Issues and Troubleshooting
Sensor Malfunction Symptoms
Engine misfires, poor fuel economy, and difficulty starting are common symptoms of a faulty crankshaft position sensor. Using the sensor diagram can aid in precise troubleshooting.
Diagnostic Tools
A multimeter and an OBD-II scanner are essential tools. Compare the sensor’s output to its expected values as per the sensor diagram.
- Check for stored trouble codes
- Inspect the physical condition of the sensor and wiring
Common Causes of Failure
Heat and vibration are primary enemies of these sensors. Over time, they can cause internal circuitry to fail. Additionally, physical damage to the wiring harness can interrupt signals.
Installation and Replacement Guide
Safety First
- Disconnect the vehicle’s battery before beginning any work.
- Ensure the engine is cool to avoid burns.
Step-by-Step Procedure
- Locate the Sensor: Refer to your vehicle’s service manual and use the crankshaft position sensor diagram as a guide.
- Disconnect the Wiring Harness: Carefully remove any clips or fasteners.
- Remove the Old Sensor: Usually held in place by bolts, unscrew these and remove the sensor.
- Install the New Sensor: Position it correctly and secure it with bolts.
- Reconnect the Wiring Harness: Ensure all electrical connections are secure.
- Test the New Sensor: Reconnect the battery and start the vehicle. Use an OBD-II scanner to check for errors.
Testing After Installation
After installing the new sensor, always test for optimal performance:
- Check for error codes
- Ensure smooth engine start and idle
- Observe fuel efficiency
Advanced Tips
Upgrading Your Sensor
Upgrading from an OEM sensor to a high-performance aftermarket sensor can yield better accuracy and durability. Refer to manufacturer websites like Bosch for options.
Fine-Tuning
Professional tuners often adjust ECU settings to get the most out of a new sensor. This can be done using specialized software and tools.
Frequently Asked Questions (FAQs)
1. What does a crankshaft position sensor do?
The sensor monitors the position and rotational speed of the crankshaft, sending data to the ECU to manage engine timing.
2. What are common symptoms of a faulty crankshaft position sensor?
Common symptoms include engine misfires, poor fuel economy, difficulty starting, and stalling.
3. Can I replace a crankshaft position sensor myself?
Yes, with basic tools and the correct sensor diagram, you can replace the sensor yourself. Always refer to your vehicle’s service manual.
4. How long does a crankshaft position sensor last?
Typically, these sensors last between 50,000 to 100,000 miles but may vary based on driving conditions and vehicle maintenance.
5. Do I need special tools to test a crankshaft position sensor?
A multimeter and an OBD-II scanner are essential tools for testing. They help in comparing the sensor’s output with the expected values.
Conclusion
Understanding and effectively using a crankshaft position sensor diagram can significantly improve your vehicle’s performance. Armed with this knowledge, you can confidently diagnose, troubleshoot, and replace the sensor, ensuring smooth engine operation. Whether you’re a seasoned mechanic or a car enthusiast, this guide offers valuable insights to help you achieve optimal performance.