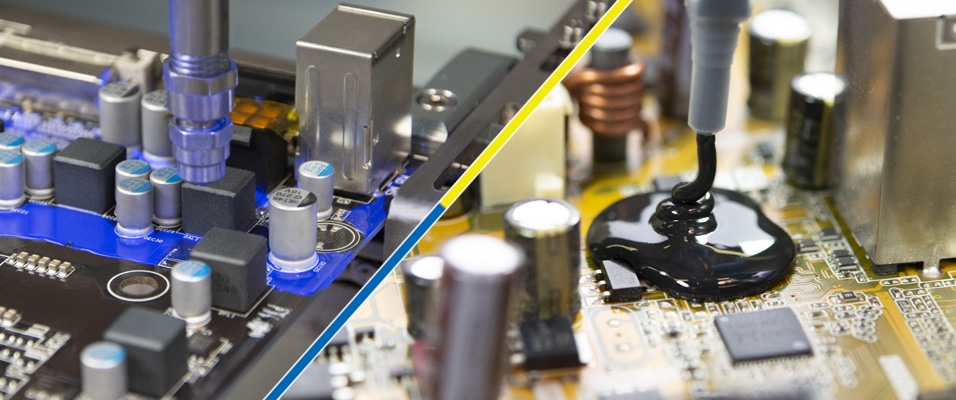
Types of conformal coating: PCB assembly protection materials
Modern devices, appliances and machinery are working in various environments and many of them are not auspicious for sensitive electronic components. Exposure to high humidity, liquids, chemical substances, dust, extreme temperatures or frequently changing temperatures can lead to quick degradation of a PCBA. Conformal coating is the most common method for protection of this essential electronic component.
Types of conformal coating: PCB assembly protection materials
The most commonly used modern protective materials are resins such as AR (acrylic resin), SR (silicone resin) and UR (polyurethane resin). Others are epoxies, poly-para-xylelene (C, D, N types), fluorinated poly-para-xylelene and amorphous fluoropolymer.
The choice of the best substance for a Printed Circuit Board (PCB) depends on the environment of its application. All of the materials used for coating have their advantages and disadvantages. For instance, solvent, moisture and abrasion-resistant UR with its great dielectric properties is also a flammable material potentially dangerous for health.
Conformal coating technologies for low-volume production
The simplest way of applying a protective material on a circuit board is with brushing. While this option requires manual labour and does not give a cosmetically appealing result, it is handy for working with a small batch of PCBs, especially for their repair or rework.
Another method frequently used for low-volume production is spraying. Instead of a brush, this method deploys an aerosol spray. Although this method gives a better surface finish than brushing, it requires thorough preparation, as the board parts that cannot be covered by the coating material should be masked first. In addition to it, it is more difficult to achieve deep penetration of a PCB.
Conformal coating technologies for high-volume production
High-volume production relies on faster methods for conformal coating. PCB assemblages requiring both-side protection can be treated with a dipping method. With this technology, a board is submerged in the solution of a coating substance and withdrawn afterwards. While this gives accurate and rapid results, it includes a step of thorough masking of the assembly regions to avoid leakage.
It is possible to reduce the amount of work, which is particularly useful for high-volume production with programmable robotic spray nozzles. These can coat exactly the spots of the board that need this protection. The method is known as selective coating.
Conclusions
PCB assemblies earmarked for working under harsh conditions require conformal coating. PCB protection materials are available in a vast variety, albeit, there are no universal products that will protect the electronics in all possible environments. The choice of the right material will always include a tradeoff between their capacities and limitations.
Coating technologies range from a basic manual brushing technique to a highly automated selective method.
Assel is a proficient PCB provider, to learn more about Printed Circuit Board (PCB) Assembly go to: Asselems.com