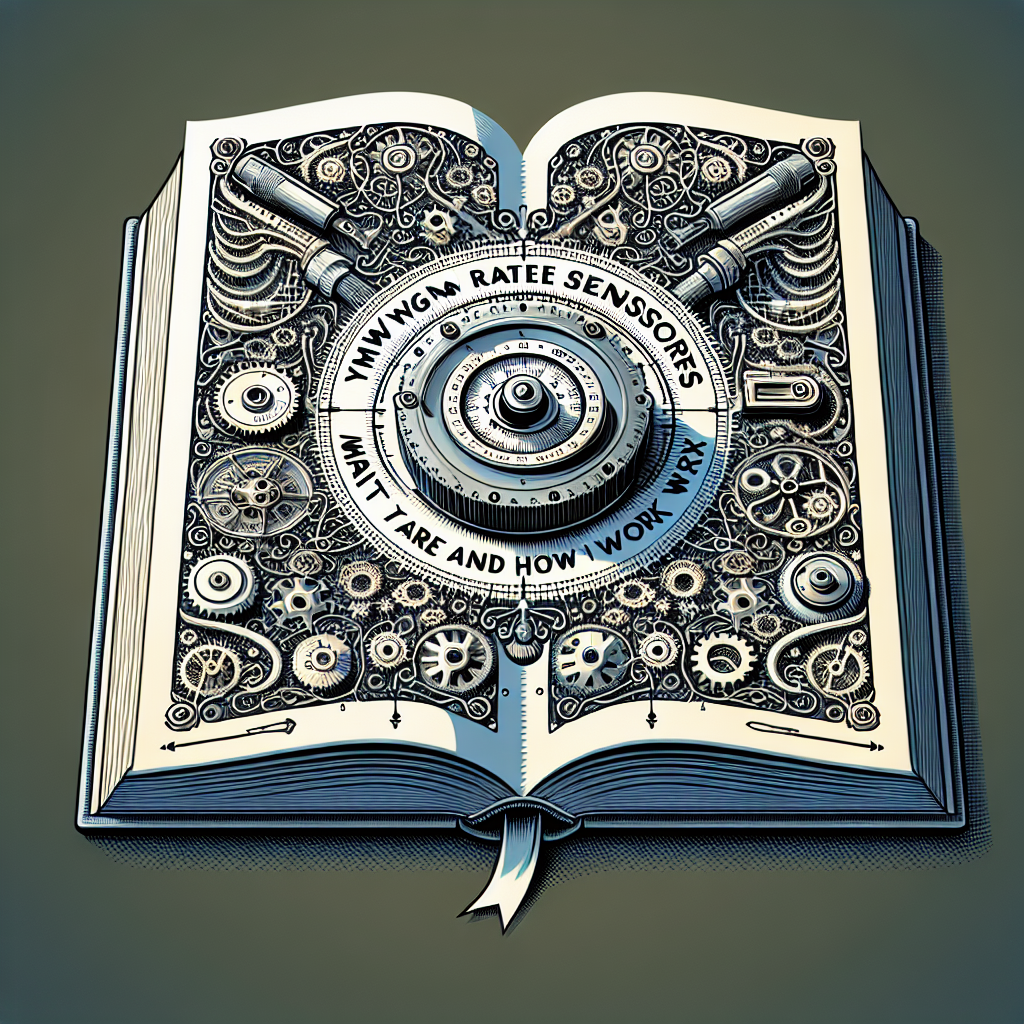
Yaw rate sensors play an essential role in modern automotive and aerospace industries. These devices help measure the angular velocity of a vehicle, contributing to better handling, stability, and safety. Given their significance, understanding yaw rate sensors, their function, and their application is crucial for anyone interested in vehicle dynamics or electronics.
What is a Yaw Rate Sensor?
A yaw rate sensor, also known as a gyroscopic sensor, is a device that measures the angular velocity around a vehicle’s vertical axis. This measurement is fundamental in detecting the rotational behavior of a vehicle, which can deeply influence its stability and control. In essence, yaw rate sensors help in understanding how a vehicle is turning relative to its steady state.
Where is the Yaw Rate Sensor Located?
Yaw rate sensors are strategically positioned in vehicles to ensure accurate readings. In most automobiles, they are placed near the vehicle’s center of gravity, often under the driver’s seat or in the central console. This central placement ensures that the sensor captures the most accurate data regarding the vehicle’s rotational movements.
How Do Yaw Rate Sensors Work?
Yaw rate sensors operate based on gyroscopic principles. They measure the rate of change of the vehicle’s angular position over time. This information is crucial for the vehicle’s stability control system. When a vehicle turns, the yaw rate sensor detects the rotational speed and direction, providing data to the vehicle’s control systems to maintain stability and control.
The Science Behind Yaw Rate Sensors
Gyroscopic Effect: Yaw rate sensors use the gyroscopic effect, which involves the principles of angular momentum and rotational motion. When the vehicle turns, the sensor detects the change in angular velocity and transmits this information to the vehicle’s Electronic Stability Control (ESC) system.
Types of Yaw Rate Sensors: There are various types of yaw rate sensors, each with unique advantages. The main types include:
- Vibratory Gyroscopes
- Optical Gyroscopes
- MEMS (Micro-Electro-Mechanical Systems) Gyroscopes
Different Types of Yaw Rate Sensors
Vibratory Gyroscopes
Vibratory gyroscopes use vibrating elements to detect angular velocity. They are often favored for their reliability and simplicity. When the vehicle turns, the vibration pattern changes, which the sensor converts into yaw rate data.
Advantages of Vibratory Gyroscopes:
- Robustness: They are less susceptible to damage from external impacts.
- Accuracy: Provide precise measurements in various conditions.
Optical Gyroscopes
Optical gyroscopes utilize light waves to measure angular velocity. They operate based on the Sagnac effect, where a phase shift occurs in light beams due to rotation. These sensors are highly sensitive and are often used in more demanding applications.
Advantages of Optical Gyroscopes:
- High Precision: Ideal for applications that require extremely accurate measurements.
- Long-term Stability: They exhibit minimal drift over time.
MEMS Gyroscopes
MEMS gyroscopes are the most widely used in automotive applications. They use miniature mechanical elements to detect rotation. The small size and cost-effectiveness of MEMS gyroscopes make them highly popular.
Advantages of MEMS Gyroscopes:
- Cost-effective: Affordable to produce and integrate into vehicles.
- Compact Size: Easy to fit within the constrained spaces of modern vehicles.
How Yaw Rate Sensors Integrate with Vehicle Systems
Yaw rate sensors do not operate in isolation; they are a part of a larger vehicle dynamics control system. These sensors work in conjunction with other sensors and control systems to enhance vehicle safety and performance.
Electronic Stability Control (ESC)
ESC is one of the primary systems that rely on yaw rate sensors. This system uses the data from the yaw rate sensor to determine if the vehicle is beginning to lose stability. If a skid or loss of traction is detected, ESC can automatically apply the brakes to individual wheels or reduce engine power to help the driver regain control.
Anti-lock Braking System (ABS)
ABS systems also benefit from yaw rate sensor data. During hard braking, if the vehicle begins to rotate, ABS can modulate brake pressure to specific wheels to maintain stability and prevent skidding.
Traction Control System (TCS)
Traction Control Systems use yaw rate sensor data to monitor tire slippage. If the sensor detects excessive yaw, indicating a potential loss of traction, the system can adjust engine power or apply brakes to specific wheels to maintain control.
Real-world Applications of Yaw Rate Sensors
Yaw rate sensors are employed in various real-world scenarios, enhancing the safety and performance of different vehicles. Understanding these applications provides insight into their significant role in modern transportation.
Automotive Applications
Modern cars, trucks, and SUVs use yaw rate sensors extensively in their stability control, anti-lock braking, and traction control systems. These sensors contribute to safer driving experiences by preventing skids, spins, and rollovers.
Aerospace Applications
In the aerospace industry, yaw rate sensors are crucial for flight control systems. They help maintain aircraft stability and provide critical data for navigation systems. Pilots rely on these sensors to ensure smooth and safe flights.
Marine Applications
Ships and boats use yaw rate sensors to aid in navigation and stability control. These sensors are particularly important in rough seas, where maintaining balance and direction is challenging.
Installation and Calibration of Yaw Rate Sensors
Proper installation and calibration of yaw rate sensors are paramount to their effectiveness. Incorrect setup or calibration can lead to inaccurate readings and compromised vehicle safety.
Installation Guidelines
- Locate an ideal mounting location: As mentioned, yaw rate sensors should be placed near the vehicle’s center of gravity.
- Secure installation: Ensure the sensor is firmly mounted to avoid vibrations that could affect its accuracy.
- Proper wiring: Connect the sensor to the vehicle’s control systems following manufacturer specifications.
Calibration Procedures
Calibrating yaw rate sensors is a crucial step in ensuring accurate data. Calibration involves setting the sensor to a known reference point and verifying its readings. Most modern vehicles come with built-in calibration procedures accessible through the vehicle’s onboard diagnostics (OBD) system.
Troubleshooting Common Yaw Rate Sensor Issues
Like any electronic component, yaw rate sensors can encounter issues. Identifying and resolving these problems is key to maintaining vehicle safety and performance.
Common Issues
- Faulty readings: Inaccurate readings can result from sensor damage or improper calibration.
- Sensor Failure: Over time, sensors can wear out or get damaged due to external factors.
- Interference: Electromagnetic interference from other vehicle components can affect sensor performance.
Troubleshooting Steps
- Check for Fault Codes: Use an OBD scanner to check for any fault codes related to the yaw rate sensor.
- Inspect the Sensor: Physically inspect the sensor for any signs of damage or wear.
- Recalibrate: If the sensor is providing faulty readings, try recalibrating it using the vehicle’s diagnostic tools.
- Replace if Necessary: If the sensor is damaged or worn out, it will need to be replaced.
Advancements in Yaw Rate Sensor Technology
As technology advances, so do yaw rate sensors. New developments are constantly improving their accuracy, reliability, and integration with vehicle control systems.
MEMS Technology Improvements
MEMS gyroscopes continue to evolve, with advancements leading to smaller, more accurate sensors. These improvements allow for better integration in modern vehicles without compromising performance.
Integration with Autonomous Vehicle Systems
Yaw rate sensors are becoming increasingly important in autonomous vehicles. They provide critical data that helps these vehicles navigate and maintain stability without human intervention.
Enhanced Signal Processing
Modern yaw rate sensors benefit from enhanced signal processing capabilities. These improvements allow for more accurate and faster readings, contributing to better vehicle control and safety.
Benefits of Using Yaw Rate Sensors
Understanding the benefits of yaw rate sensors underscores their importance in modern vehicles. These sensors significantly enhance vehicle safety, performance, and driver confidence.
Enhanced Vehicle Stability
Yaw rate sensors play a crucial role in maintaining vehicle stability. By providing accurate data on the vehicle’s rotational movements, they help prevent skids and rollovers.
Improved Safety Systems
Safety systems like ESC, ABS, and TCS rely on yaw rate sensors. These systems enhance vehicle safety by preventing accidents and improving control during challenging driving conditions.
Better Handling and Performance
Vehicles equipped with yaw rate sensors offer better handling and performance. Drivers experience more precise control, especially during turns and maneuvers, leading to a more enjoyable driving experience.
Conclusion
Yaw rate sensors are indispensable in modern vehicle safety and control systems. They provide critical data that enhances vehicle stability, safety, and performance. Understanding how they work, their applications, and their integration with vehicle systems is essential for anyone interested in automotive technology. Whether you’re a driver, mechanic, or engineer, knowing about yaw rate sensors can help you appreciate the sophisticated engineering that goes into modern vehicles.
Frequently Asked Questions (FAQs)
1. What is a yaw rate sensor, and why is it important?
A yaw rate sensor measures the angular velocity around a vehicle’s vertical axis, helping to detect rotational behavior. It is crucial for vehicle stability and control systems, which enhance safety and performance.
2. How do yaw rate sensors work in conjunction with Electronic Stability Control (ESC)?
Yaw rate sensors provide ESC systems with data about the vehicle’s rotational movements. ESC uses this data to apply brakes or reduce engine power, helping to maintain vehicle stability during maneuvers.
3. Can a faulty yaw rate sensor affect vehicle safety?
Yes, a faulty yaw rate sensor can provide incorrect data to stability and control systems, potentially compromising vehicle safety. It is essential to troubleshoot and replace faulty sensors to maintain optimal safety.
4. Are yaw rate sensors used in applications outside of automotive?
Yes, yaw rate sensors are also used in aerospace and marine applications. They help in maintaining stability and navigation for aircraft and boats, similarly to how they enhance vehicle safety and performance.
For more information on yaw rate sensors and their applications, you can visit:
- Safer Car: Importance of Vehicle Sensors
- Automotive Technology Explained
- MEMS Gyroscopes in Automotive
Feel free to dive deeper into these resources for additional insights on the fascinating world of yaw rate sensors and their contributions to modern technology.